Manutenção e Instalação Industrial: Guia Completo
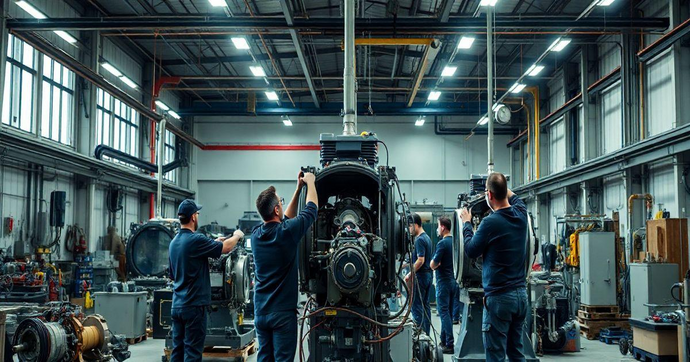
Por: Gabriel - 29 de Dezembro de 2024
Manutenção e instalação industrial são fundamentais para garantir a operação eficiente de qualquer empreendimento. Esses processos asseguram que máquinas e equipamentos funcionem de forma ideal, minimizando paradas imprevistas e aumentando a produtividade. Neste artigo, você aprenderá sobre a importância desses serviços, as diversas estratégias de manutenção disponíveis e como realizar instalações seguras e eficazes. Continue lendo para se aprofundar em boas práticas e enfrentar os desafios do setor de forma eficaz.
Importância da Manutenção e Instalação Industrial
A manutenção e instalação industrial desempenham um papel crucial na vida útil e eficiência dos equipamentos em diversos setores. Estas práticas não apenas garantem que as máquinas funcionem adequadamente, mas também previnem problemas que podem resultar em interrupções na produção e prejuízos financeiros. É essencial compreender a importância dessas atividades, pois elas afetam diretamente a performance das operações industriais.
Um dos principais benefícios da manutenção industrial é a redução de custos a longo prazo. A manutenção preventiva, por exemplo, ajuda a identificar e corrigir problemas antes que se tornem maiores. Isso não apenas evita que os equipamentos quebrem, mas também reduz a necessidade de reparos caros e emergenciais. Ao investir em manutenção regularmente, as empresas podem economizar significantemente em substituições e paralisações não programadas.
Além da economia, a manutenção eficaz melhora a segurança dos trabalhadores. Equipamentos que não são mantidos adequadamente podem se tornar perigosos, aumentando o risco de acidentes de trabalho. Ao assegurar que as máquinas estejam sempre em boas condições, as empresas promovem um ambiente de trabalho mais seguro, o que é fundamental para proteger a saúde dos seus colaboradores.
Outro aspecto importante a ser mencionado é o impacto da manutenção e instalação industrial na eficiência operacional. Equipamentos em bom estado tendem a operar com maior produtividade e precisão. Isso significa que as empresas podem atender à demanda dos clientes de maneira mais eficaz, mantendo a qualidade dos produtos oferecidos. Em um mercado competitivo, a eficiência pode ser um diferencial significativo e pode levar a um aumento na satisfação do cliente.
A instalação correta de novos equipamentos é igualmente vital. Uma instalação inadequada pode resultar em falhas de funcionamento ou até danos aos sistemas existentes. É necessário seguir as diretrizes do fabricante e contar com profissionais qualificados para garantir que cada fase da instalação seja realizada corretamente. Isso ajuda a maximizar o desempenho do novo equipamento e a evitar problemas no futuro.
Além disso, a manutenção e instalação industrial têm um papel importante na sustentabilidade. Equipamentos que são mantidos corretamente consomem menos energia e recursos, contribuindo para a redução da pegada ambiental da empresa. A utilização de recursos de forma eficiente é não apenas uma responsabilidade social, mas também uma oportunidade para as empresas se posicionarem como líderes em sustentabilidade dentro do seu setor.
As empresas devem também considerar a integração de tecnologias modernas na manutenção e instalação industrial. Isso inclui o uso de software especializado para monitoramento de equipamentos, que pode alertar as equipes sobre a necessidade de manutenção antes que um problema ocorra. A adoção de tecnologias pode aumentar a eficácia desse processo e permitir uma gestão mais eficiente das operações industriais.
Por fim, outro ponto de relevância é a continuidade dos negócios. Interrupções na operação podem ser extremamente prejudiciais, causando demoras e impactos financeiros significativos. Um programa de manutenção robusto garante que os sistemas estejam sempre operacionais e prontos para atender a demanda, minimizando riscos e proporcionando uma base sólida para o crescimento do negócio.
Portanto, a manutenção e instalação industrial são mais do que simples atividades operacionais: são investimentos estratégicos que impactam a eficiência, segurança e sustentabilidade das operações. Para garantir que todas essas práticas sejam aplicadas de maneira correta, contar com profissionais qualificados e fornecedores confiáveis é fundamental. Por exemplo, ao buscar componentes e materiais, considere uma Distribuidora de aço inox que atenda a padrões elevados de qualidade.
Em resumo, a manutenção e instalação industrial devem ser tratadas como uma prioridade nas empresas que desejam manter sua competitividade no mercado. Investir nestas áreas não apenas protege os ativos, mas também promove um ambiente de trabalho seguro e eficiente, contribuindo para o sucesso a longo prazo da organização.
Tipos de Manutenção: Preventiva, Corretiva e Preditiva
A manutenção industrial é um aspecto fundamental para garantir a eficiência, segurança e longevidade dos equipamentos utilizados nas indústrias. Existem diferentes tipos de manutenção que podem ser empregados, cada um com suas características e aplicações. Os três tipos mais comuns são a manutenção preventiva, a manutenção corretiva e a manutenção preditiva. Compreender as diferenças entre esses métodos é essencial para implementar uma estratégia eficaz de manutenção em sua operação industrial.
A manutenção preventiva é uma abordagem proativa que busca evitar falhas nos equipamentos antes que elas ocorram. Ela envolve atividades programadas, como inspeção, lubrificação e substituição de peças, que são realizadas em intervalos definidos. O principal objetivo da manutenção preventiva é prolongar a vida útil dos equipamentos e minimizar o risco de paradas inesperadas. Essa abordagem pode resultar em uma maior eficiência operacional, pois os problemas são identificados e corrigidos antes que possam afetar a produção.
Um dos benefícios da manutenção preventiva é a redução de custos a longo prazo. Ao adotar um cronograma de manutenção regular, as empresas podem evitar os altos custos associados a reparos emergenciais e substituições. Isso é especialmente relevante em indústrias onde o tempo de inatividade pode resultar em perdas financeiras significativas. Além disso, a manutenção preventiva contribui para a segurança dos trabalhadores, uma vez que equipamentos bem mantidos são menos propensos a falhas que podem causar acidentes.
Por outro lado, a manutenção corretiva é realizada após a ocorrência de uma falha ou mau funcionamento no equipamento. Nesse caso, o objetivo é restaurar o equipamento à sua condição operacional o mais rápido possível. Muitas vezes, as empresas que não implementam um bom plano de manutenção preventiva acabam recorrendo mais frequentemente à manutenção corretiva, o que pode ser dispendioso e prejudicar a produtividade. As manutenções corretivas podem ser classificadas em dois tipos: a manutenção corretiva simples, que é a reparação de avarias, e a manutenção corretiva complexa, que pode exigir a reestruturação completa do sistema danificado.
Embora a manutenção corretiva seja inevitável em algumas situações, confiar nela como a única estratégia de manutenção pode levar a um ciclo vicioso de falhas e reparos constantes. Os custos associados a esse método podem aumentar rapidamente, especialmente se a produção for interrompida por longos períodos. Portanto, tentar equilibrar a manutenção corretiva com a preventiva é uma estratégia que muitas empresas bem-sucedidas adotam para evitar essas armadilhas.
A manutenção preditiva, por sua vez, é uma abordagem moderna que utiliza tecnologia avançada para monitorar o estado dos equipamentos em tempo real. Essa modalidade se baseia na coleta e análise de dados para prever quando um problema pode ocorrer, permitindo que a manutenção seja realizada apenas quando necessário. Isso é possível por meio do uso de sensores e sistemas de monitoramento, que detectam mudanças no desempenho dos equipamentos que possam indicar um desgaste ou falha iminente.
Uma das principais vantagens da manutenção preditiva é a capacidade de otimizar os recursos. Ao realizar a manutenção apenas quando necessário, as empresas podem economizar tempo e dinheiro, evitando manutenções desnecessárias. Além disso, a manutenção preditiva pode ajudar a maximizar a produção, pois reduz o número de paradas não programadas e permite que os equipamentos operem em suas melhores condições por períodos mais longos.
Para obter o máximo benefício dos tipos de manutenção, é recomendável que as empresas adotem um enfoque integrado. Combinar a manutenção preventiva com a manutenção preditiva, por exemplo, pode fornecer uma abordagem abrangente que alinha a segurança e eficiência. Isso envolve utilizar a manutenção preventiva para garantir que os sistemas estejam sempre em bom estado, enquanto a preditiva fornece dados valiosos que podem ser usados para decisões informadas sobre quando realizar intervenções.
Além disso, quando as empresas buscam serviços de instalação, é importante contar com parceiros confiáveis. Se você está procurando por uma solução abrangente na área de montagem, considere contar com uma Empresa de montagem de estrutura metálica que atue com excelência e compromisso na entrega de serviços de qualidade.
Em conclusão, conhecer os diferentes tipos de manutenção é fundamental para a gestão eficaz dos processos industriais. A manutenção preventiva, corretiva e preditiva apresentam vantagens e desvantagens que precisam ser ponderadas para criar um sistema de manutenção que maximize a operação e minimize custos. Avaliar a estratégia existente e considerar ajustes pode levar a uma operação mais eficiente e segura, beneficiando não apenas a empresa, mas também seus colaboradores e clientes.
Ferramentas Necessárias para Instalação Industrial
Na instalação industrial, a escolha das ferramentas corretas é fundamental para garantir a eficiência, a segurança e a qualidade do trabalho realizado. Uma boa instalação não depende apenas das habilidades dos profissionais envolvidos, mas também do uso adequado de equipamentos e ferramentas específicas. Neste artigo, abordaremos algumas das ferramentas essenciais para a instalação industrial, destacando a importância de cada uma e como elas contribuem para o sucesso do projeto.
Uma das ferramentas mais fundamentais para qualquer instalação industrial é a chave de fenda. Ela é utilizada para apertar ou soltar parafusos e, dependendo do tipo de chave, pode ser utilizada em uma variedade de tamanhos e formatos de parafusos. A versatilidade das chaves de fenda as torna indispensáveis em inúmeras aplicações, oferecendo praticidade e eficiência na montagem de estruturas e equipamentos.
Além disso, a chave inglesa é outra ferramenta essencial que se destaca pela sua capacidade de ajuste. Com ela, é possível trabalhar com diferentes tamanhos de porcas e parafusos, o que a torna uma opção bastante útil em instalações que envolvem diversas peças e componentes. A chave inglesa facilita o processo de montagem e desmontagem, aumentando a agilidade nas operações.
As ferramentas de medição, como o nível e a fita métrica, são igualmente importantes na instalação industrial. O nível é crucial para garantir que os equipamentos sejam instalados de forma alinhada e estável, prevenindo problemas estruturais e aumentando a segurança. Já a fita métrica permite que os profissionais façam medições precisas, o que é essencial para assegurar que as peças se encaixem corretamente e que a estrutura atenda às especificações necessárias.
Outra ferramenta vital é a furadeira. Essa máquina é utilizada para perfurar materiais, como metal e madeira, permitindo a instalação de suportes, ancoragens e outros componentes essenciais. As furadeiras estão disponíveis em várias versões, incluindo furadeiras manuais e elétricas, oferecendo diversas funcionalidades que podem atender a diferentes necessidades de instalação.
Quando se trata de instalação de estruturas metálicas, ter acesso a um cortador de metais é crucial. Esses cortadores podem ser manuais ou elétricos e são projetados para fazer cortes precisos em materiais metálicos, facilitando a montagem de estruturas industriais. Um bom cortador de metais garante que as peças se ajustem perfeitamente, otimizando o tempo de instalação e a qualidade do trabalho.
As máquinas de solda também são indispensáveis na instalação industrial, especialmente quando se trabalha com estruturas metálicas. Elas permitem que os profissionais unam diferentes componentes, criando estruturas robustas e seguras. A escolha do tipo de solda, como MIG, TIG ou eletrodos revestidos, dependerá do material utilizado e das especificações do projeto.
Além das ferramentas manuais e elétricas, o uso de equipamentos de proteção individual (EPIs) é essencial durante a instalação industrial. O uso adequado de EPIs, como capacetes, luvas, óculos de segurança e protetores auriculares, ajuda a garantir a segurança dos trabalhadores em ambientes potencialmente perigosos. A segurança deve ser sempre uma prioridade em qualquer instalação industrial.
Durante o processo de instalação, os profissionais podem também precisar de aparelhos de medição digitais, como multímetros e termômetros infravermelhos, para garantir que as condições elétricas e térmicas estejam dentro dos parâmetros adequados. Esses dispositivos permitem a realização de medições precisas que são fundamentais para a segurança e eficiência dos sistemas instalados.
Não podemos esquecer da importância de um bom organizador de ferramentas, que pode ajudar a manter o local de trabalho limpo e organizado. Ter as ferramentas à mão e bem organizadas melhora significativamente a eficiência do trabalho e reduz o tempo perdido na procura por equipamentos. Um local de trabalho bem gerenciado é sinônimo de maior produtividade e segurança.
Por último, ao selecionar ferramentas para suas instalações, é fundamental escolher fornecedores confiáveis que ofereçam produtos de alta qualidade. Para isso, você pode considerar um comércio de aço inox que forneça os materiais e ferramentas necessárias, garantindo que você tenha acesso ao que há de melhor no mercado.
Em resumo, a instalação industrial exige a combinação de diversas ferramentas e equipamentos para garantir que o trabalho seja realizado com eficiência e segurança. Desde chaves de fenda e chaves inglesas até cortadores de metais e máquinas de solda, cada ferramenta desempenha um papel vital no processo. Investir em ferramentas de qualidade e treinamento adequado para a equipe não apenas resulta em um projeto de instalação bem-sucedido, mas também promove um ambiente de trabalho seguro e produtivo.
Processos de Instalação: Passo a Passo
Os processos de instalação industrial são fundamentais para garantir que todos os equipamentos e estruturas estejam corretamente montados e funcionando de acordo com as especificações projetadas. Esse processo deve ser realizado com cuidado e atenção aos detalhes, já que qualquer erro pode resultar em problemas sérios no funcionamento dos sistemas, além de comprometer a segurança dos trabalhadores. Neste artigo, abordaremos o passo a passo para uma instalação industrial eficiente e organizada.
O primeiro passo em qualquer processo de instalação é a planejamento e preparação. Isso envolve a definição clara das metas e objetivos da instalação, bem como a elaboração de um cronograma que indique todas as etapas do projeto. Também é crucial realizar uma análise detalhada do local onde a instalação ocorrerá. Isso inclui a verificação de medidas, condições do terreno, infraestrutura existente e fatores que possam afetar o projeto, como acesso a serviços essenciais e segurança.
Paralelamente, deve-se considerar a reunião da equipe envolvida no processo de instalação. Essa equipe pode incluir engenheiros, técnicos, eletricistas e operadores, dependendo da complexidade do projeto. Uma comunicação clara e eficaz entre todos os membros da equipe é essencial para o sucesso da instalação, e isso muitas vezes é alcançado através de reuniões preparatórias para discutir o planejamento e as funções de cada um.
Em seguida, o próximo passo é obter as ferramentas e materiais necessários. Isso envolve garantir que todas as ferramentas, equipamentos e peças estejam disponíveis e em boas condições de uso. Ter um inventário detalhado de ferramentas e materiais pode ajudar a evitar atrasos devido à falta de equipamentos essenciais. Planejar a logística de entrega de materiais também é fundamental para garantir que tudo esteja no local de trabalho quando necessário, evitando interrupções desnecessárias no cronograma.
Uma vez que todo o planejamento e preparação estejam concluídos, é hora de proceder com a instalação propriamente dita. O processo de instalação pode variar dependendo do tipo de equipamento ou estrutura a ser montada, mas algumas etapas gerais devem ser seguidas. No caso de estruturas metálicas, por exemplo, a primeira etapa pode envolver a montagem da base ou fundação. Essa etapa é crucial, pois a fundação precisa estar nivelada e capaz de suportar o peso da estrutura que será instalada.
Após a finalização da fundação, passa-se à montagem das estruturas principais. Isso envolve unir os diferentes componentes metálicos, como vigas e colunas, utilizando técnicas adequadas de soldagem, parafusamento ou outros métodos de ancoragem. É importante seguir as especificações de projeto durante esta fase, garantindo que as peças estejam alinhadas corretamente e que todas as conexões sejam seguras. O uso de ferramentas de medição, como níveis e esquadros, é essencial para garantir que a estrutura esteja estável e dentro dos parâmetros especificados.
Uma vez que as estruturas principais estão no lugar, o próximo passo é instalar componentes auxiliares, como sistemas elétricos, hidráulicos e pneumáticos, se aplicável. Esta fase pode incluir a fiação de máquinas, a instalação de sistemas de tubulação e a conexão de equipamentos. É vital que essa etapa seja realizada por profissionais qualificados para garantir que todos os sistemas estejam seguros e funcionais, evitando problemas futuros que possam afetar a operação da instalação.
Depois de concluir a instalação física, o próximo passo é realizar testes de funcionalidade e segurança. Isso pode incluir testes de desempenho das máquinas, verificação de sistemas elétricos e a realização de inspeções de segurança. É fundamental que todos os testes sejam realizados antes da entrega final do projeto, garantindo que qualquer problema seja identificado e corrigido antes que a instalação entre em operação. A documentação desses testes é igualmente importante, pois pode servir como referência futura em manutenção e inspeções.
Quando todas as etapas são concluídas com sucesso, é essencial realizar um treinamento da equipe de operação. Esse treinamento deve abranger não apenas como operar os novos equipamentos, mas também como realizar manutenções básicas e garantir a segurança no ambiente de trabalho. Uma equipe bem treinada e informada é um fator-chave para a eficácia da operação da instalação e para a redução de riscos de acidentes.
Por fim, ao considerar a instalação de novos sistemas industriais, contar com a expertise de uma Empresa de montagem industrial pode otimizar todos esses processos. Profissionais qualificados trazem experiência e conhecimento técnicos que garantem uma instalação segura e eficiente.
Em resumo, os processos de instalação industrial envolvem um planejamento cuidadoso, a reunião de uma equipe qualificada, a obtenção das ferramentas necessárias e a execução de etapas detalhadas para garantir uma instalação eficiente e segura. Ao seguir cada uma dessas etapas, as empresas podem garantir que suas instalações operem de maneira ideal, maximizando produtividade e segurança no ambiente de trabalho.
Desafios Comuns na Manutenção Industrial
A manutenção industrial é uma parte crucial do funcionamento de qualquer instalação, assegurando que os equipamentos operem de maneira eficiente e segura. No entanto, muitas empresas enfrentam um conjunto de desafios que podem impactar a eficácia das suas atividades de manutenção. Identificar e compreender esses desafios é o primeiro passo para abordá-los de forma eficaz e melhorar a performance operacional. Neste artigo, discutiremos alguns dos desafios comuns encontrados na manutenção industrial, bem como possíveis soluções para cada um deles.
Um dos principais desafios na manutenção industrial é a falta de planejamento. Muitas vezes, as empresas não têm um plano de manutenção estruturado, o que resulta em intervenções de última hora e manutenções reativas. Essa abordagem pode ser extremamente dispendiosa, pois a manutenção corretiva geralmente envolve custos mais altos do que a manutenção preventiva. Para contornar esse problema, é fundamental que as empresas desenvolvam um plano de manutenção abrangente que inclua programações regulares e estratégias específicas de intervenção.
Outro desafio significativo é a falta de qualificação da equipe. A manutenção industrial exige conhecimentos técnicos especializados, e a falta de pessoal qualificado pode levar a erros na execução de tarefas, atrasos e riscos de segurança. Para superar esse desafio, as empresas devem investir em treinamento contínuo para seus funcionários, assegurando que todos estejam atualizados sobre as melhores práticas e as tecnologias mais recentes utilizadas na manutenção. Além disso, oferecer programas de capacitação pode aumentar a motivação e a retenção de funcionários qualificados.
A falta de recursos e ferramentas adequadas também é um obstáculo que muitas organizações enfrentam. Se as ferramentas necessárias para realizar a manutenção não estão disponíveis ou em boas condições, a equipe pode se ver atrasada na execução de tarefas, o que pode resultar em períodos de inatividade não planejados. As empresas devem fazer um inventário regular de suas ferramentas e equipamentos, garantindo que tudo o que é necessário para a manutenção esteja em boas condições e acessível para a equipe.
Outra questão frequentemente encontrada é a ineficiência na comunicação. A comunicação deficiente entre as equipes de manutenção e operação pode levar a falhas na execução das tarefas, desentendimentos sobre prioridades e atrasos. Para melhorar a comunicação, é essencial estabelecer protocolos claros que garantam que todos os membros da equipe estejam alinhados. Reuniões regulares de acompanhamento e a utilização de softwares de gestão de manutenção podem ajudar a promover uma comunicação mais eficiente.
Aumentar a complexidade das operações industriais é uma tendência que também apresenta desafios para a manutenção. À medida que as tecnologias se tornam mais sofisticadas, as técnicas de manutenção também precisam evoluir. Isso exige que os profissionais de manutenção se especializem em sistemas mais complexos, o que pode ser um desafio em termos de treinamento e adaptação. As empresas devem abordar essa questão investindo em ferramentas de manutenção baseadas em tecnologia e capacitando suas equipes para lidar com novos sistemas e procedimentos.
Além disso, a gestão de dados é um desafio crescente na manutenção industrial. À medida que mais equipamentos são equipados com sensores e se tornam parte da Internet das Coisas (IoT), o volume de dados gerados pode ser esmagador. Saber como coletar, analisar e interpretar esses dados é crucial para a implementação de estratégias de manutenção preditiva. Para lidar com os dados gerados, as empresas devem investir em software que permita a análise adequada das informações e a tomada de decisões informadas sobre manutenções futuras.
Não menos importante, um desafio significativo são as restrições orçamentárias. Muitas organizações enfrentam pressão para reduzir custos ao mesmo tempo em que tentam manter a eficiência de suas operações. Isso pode levar a cortes em programas de manutenção preventiva e maior dependência de manutenção corretiva, resultando em custos mais altos a longo prazo. Para mitigar esse problema, as empresas podem implementar uma abordagem mais eficaz de manutenção, priorizando manutenções que têm um impacto significativo na produção e colocando recursos em áreas críticas.
Além disso, os períodos de inatividade não planejados são um dos desafios mais frustrantes na manutenção industrial. Paradas inesperadas podem resultar em perda de produção e custos elevados. Para enfrentar esse problema, as empresas devem desenvolver um bom cronograma de manutenção preventiva, bem como planejar estratégias de contingência que possam ser rapidamente implementadas quando problemas ocorrem, minimizando assim o tempo de inatividade.
Em resumo, os desafios comuns na manutenção industrial incluem falta de planejamento, equipe não qualificada, falta de recursos, comunicação ineficiente, complexidade das operações, gestão inadequada de dados, restrições orçamentárias e períodos de inatividade não planejados. Cada um desses desafios apresenta sua própria série de obstáculos, mas, uma vez identificados, podem ser endereçados com estratégias e soluções adequadas. Ao investir na melhoria das práticas de manutenção e capacitação da equipe, as empresas podem não apenas melhorar a eficiência e a segurança, mas também aumentar significativamente sua competitividade no mercado.
Benefícios de um Programa de Manutenção
Um programa de manutenção bem estruturado é essencial para o funcionamento eficiente de qualquer instalação industrial ou negócio. Muitas empresas ainda subestimam a importância da manutenção, mas existem vários benefícios que um programa de manutenção pode trazer para a operação. Neste artigo, discutiremos os principais benefícios de implementar um programa de manutenção eficaz, destacando como isso pode impactar positivamente a produtividade, a segurança e a longevidade dos equipamentos.
Um dos benefícios mais significativos de um programa de manutenção é a redução de custos. A manutenção preventiva, que faz parte de um programa bem estruturado, permite que as empresas identifiquem e resolvam problemas antes que se tornem falhas sérias. Ao evitar que equipamentos quebrem ou necessitem de reparos emergenciais, as organizações podem economizar consideravelmente em custos de manutenção corretiva e substituições. Esse custo é muitas vezes muito maior e pode impactar negativamente o orçamento da empresa.
Outro benefício importante é a aumento da eficiência operacional. A manutenção regular assegura que os equipamentos funcionem em suas melhores condições, resultando em desempenho otimizado. Isso não apenas melhora a capacidade produtiva da empresa, mas também aumenta a qualidade dos produtos e serviços. Equipamentos bem mantidos têm uma vida útil mais longa e são menos propensos a falhas, o que se traduz em menos interrupções no fluxo de trabalho e maior eficiência geral.
Além disso, a presença de um programa de manutenção pode contribuir para uma redução significativa no tempo de inatividade. Equipamentos que recebem manutenção regular têm menos probabilidade de apresentar problemas inesperados e, consequentemente, menos períodos de inatividade. Isso não somente ajuda a manter um fluxo contínuo de produção, mas também melhora a confiabilidade da operação, assegurando que os produtos cheguem aos clientes no prazo. A confiabilidade é um fator-chave que pode impactar a satisfação do cliente e a reputação da empresa.
Do ponto de vista da segurança do trabalho, um programa de manutenção desempenha um papel crucial na identificação e correção de riscos potenciais. Equipamentos não mantidos podem se tornar perigosos e aumentar a probabilidade de acidentes no local de trabalho. Ao garantir que máquinas e sistemas estejam em boas condições, um programa de manutenção contribui para um ambiente de trabalho mais seguro, o que é fundamental para proteger a saúde dos colaboradores e reduzir responsabilidades legais decorrentes de acidentes.
Adicionalmente, um programa de manutenção eficiente está ligado à melhoria da moral e satisfação dos funcionários. Profissionais que trabalham em um ambiente que prioriza a segurança e a eficiência tendem a estar mais motivados e satisfeitos com seu trabalho. A sensação de que estão utilizando equipamentos em boas condições e que suas preocupações estão sendo levadas em consideração pode aumentar significativamente a satisfação no trabalho e, assim, reduzir a rotatividade de pessoal.
Outro aspecto benéfico diz respeito à facilidade na identificação de falhas. Um programa de manutenção sistemático geralmente inclui a documentação detalhada de todas as intervenções realizadas nos equipamentos. Isso permite que a equipe de manutenção analise informações históricas e identifica padrões, o que pode auxiliar na formulação de estratégias para prevenir falhas recorrentes. A análise de dados também pode ajudar a identificar quais equipamentos exigem mais atenção e quais podem ser otimizados.
A implementação de um programa de manutenção também proporciona uma melhoria na conformidade regulatória. Muitas indústrias estão sujeitas a regulamentações que exigem a manutenção de equipamentos e a realização de inspeções regulares. Um programa de manutenção ajuda a garantir que os requisitos legais e normativos sejam atendidos, evitando assim penalidades e danos à reputação da empresa. Isso é particularmente importante em setores como farmacêutico, químico e alimentar, onde a conformidade é crítica.
Além disso, um programa de manutenção pode promover uma cultura de melhoria contínua dentro da organização. Quando a manutenção é vista como uma prioridade, os funcionários são incentivados a se manter atualizados em relação às melhores práticas e inovações no campo da manutenção. Isso não somente contribui para a eficiência dos processos existentes, mas também pode conduzir a inovações que melhorem ainda mais a operação.
Por último, mas não menos importante, a vantagem de um programa de manutenção é a proteção do investimento em ativos. Equipamentos e maquinários representam um investimento significativo para as empresas, e mantê-los em boas condições ajuda a preservar seu valor. Investir em manutenção regular pode evitar a depreciação rápida dos ativos e prolongar sua vida útil, garantindo que a empresa obtenha o máximo retorno sobre seu investimento.
Portanto, fica claro que os benefícios de um programa de manutenção são vastos e variados. Redução de custos, eficiência operacional, segurança, melhoria da moral dos funcionários, identificação de falhas e conformidade regulatória são apenas algumas das vantagens que esse tipo de programa pode trazer. As empresas que priorizam a manutenção não apenas protegem seus ativos, mas também criam um ambiente de trabalho que valoriza a segurança e a eficiência. Ao buscar soluções para fortalecer a manutenção, considere também um parceiro competente que possa auxiliar nesse processo, como uma empresa especializada em montagens. Essa escolha pode fazer toda a diferença na implementação de um programa eficaz, maximizando os resultados e garantindo a continuidade do sucesso operacional.
Como Escolher um Profissional de Instalação Industrial
A escolha do profissional adequado para a instalação industrial é uma etapa crítica que pode determinar o sucesso de um projeto. A complexidade das operações industriais exige trabalhadores qualificados que entendam não apenas de técnicas de instalação, mas também de segurança, eficiência e conformidade com as normas. Neste guia, abordaremos os principais critérios que devem ser considerados ao selecionar um profissional para instalação industrial.
O primeiro aspecto a ser considerado é a qualificação e experiência. Ao procurar por um profissional de instalação industrial, é essencial verificar se ele possui as certificações pertinentes e se tem uma formação adequada em sua área de atuação. Profissionais com formação técnica em engenharia, mecânica ou elétrica, por exemplo, têm um entendimento mais profundo das operações que precisam ser executadas, além de serem mais capazes de lidar com os desafios que podem surgir. A experiência anterior em projetos similares também é um fator crucial; um profissional que já trabalhou em instalações do mesmo porte ou tipo estará melhor preparado para antecipar problemas e oferecer soluções.
Além da qualificação, é importante avaliar a reputação e referências do profissional ou da empresa de instalação. Pesquisar sobre trabalhos anteriores, bem como verificar referências e depoimentos de clientes é uma prática recomendada. As avaliações online e o feedback de outros clientes podem fornecer uma visão clara sobre a qualidade do trabalho e a confiabilidade do profissional. Não hesite em pedir exemplos de projetos anteriores e buscar recomendações de colegas do setor.
O conhecimento das normas de segurança é outro ponto essencial a ser considerado. A segurança deve ser uma prioridade em qualquer operação industrial. Verifique se o profissional está familiarizado com as regulamentações e normas de segurança aplicáveis à sua indústria. Um profissional que valoriza a segurança será mais capaz de identificar potenciais riscos e implementar as práticas de trabalho seguras necessárias durante a instalação. Pedir documentação que comprove a formação em segurança pode ser um diferencial importante.
Outro fator a ser analisado é a capacidade de comunicação. A habilidade de se comunicar efetivamente com a equipe de trabalho e os gestores é fundamental para o sucesso da instalação industrial. O profissional deve ser capaz de entender as necessidades específicas do projeto e ser claro na transmissão de instruções e informações. Uma boa comunicação pode evitar mal-entendidos, economizando tempo e recursos durante o processo.
Além disso, considere a flexibilidade e a disponibilidade do profissional. Instalações industriais podem exigir trabalho em horários não convencionais ou em prazos apertados. Certifique-se de que o profissional que você escolher tenha a capacidade de se adaptar a mudanças de cronograma e esteja disponível quando necessário. Também é importante que ele seja proativo e comprometido em cumprir prazos e superar expectativas.
Os custos e orçamentos também desempenham um papel crucial na escolha de um profissional de instalação. É importante obter orçamentos detalhados de diferentes prestadores de serviços, levando em consideração não apenas o custo, mas também o que está incluído no serviço. Um preço mais baixo pode parecer atraente, mas é fundamental avaliar a qualidade e a abrangência do serviço oferecido. Além disso, esteja atento a custos ocultos que possam surgir ao longo do processo de instalação.
É recomendável que, antes de tomar a decisão final, você realize uma entrevista pessoal com o profissional ou equipe de instalação. Essa interação pode proporcionar uma visão mais clara sobre a atitude, conhecimento e abordagem do profissional em relação ao trabalho. Uma conversa direta pode ajudar a esclarecer dúvidas, discutir detalhes do projeto e descobrir a visão do profissional sobre a instalação. Essa etapa é crucial para garantir que você e o profissional estejam alinhados em relação às expectativas e à abordagem do projeto.
Não menos importante é a verificação do apoio pós-instalação. Um bom profissional deve oferecer suporte após a conclusão da instalação, incluindo serviços de manutenção, assistência técnica e o fornecimento de garantias. O suporte pós-instalação é fundamental para garantir que os sistemas permaneçam operacionais e que quaisquer problemas que possam surgir sejam tratados de forma rápida e eficiente.
Por fim, ao considerar a escolha de um profissional ou empresa para a instalação industrial, não se esqueça da importância da experiência da sua escolhida em trabalhar com um empresa especializada em montagens. A escolha de um parceiro confiável e experiente pode facilitar muito todo o processo e garantir que o trabalho seja realizado com profissionalismo e eficiência.
Em resumo, a escolha de um profissional de instalação industrial deve ser feita com cuidado e atenção a detalhes essenciais, como qualificação, experiência, reputação, segurança, comunicação, flexibilidade, custos e suporte pós-instalação. Tomar decisões informadas pode não apenas garantir o sucesso do projeto, mas também contribuir para um ambiente de trabalho mais seguro e produtivo. Ao seguir essas diretrizes, você poderá encontrar o profissional ideal para atender às suas necessidades de instalação industrial com excelência.
Tendências Futuras em Manutenção e Instalação Industrial
O campo da manutenção e instalação industrial está em constante evolução, impulsionado pelas inovações tecnológicas e pela crescente necessidade de eficiência e segurança nas operações industriais. À medida que nos aproximamos de um futuro cada vez mais digital e conectado, diversas tendências estão se destacando, moldando o modo como as indústrias realizam suas tarefas de manutenção e instalação. Neste artigo, discutiremos as principais tendências que estão moldando o futuro da manutenção e instalação industrial.
Uma das tendências mais significativas é a manutenção preditiva, que utiliza dados em tempo real para prever falhas antes que elas ocorram. Graças à adoção de sensores e dispositivos IoT (Internet das Coisas), as empresas podem coletar dados de desempenho de máquinas e equipamentos em tempo real. Isso permite a análise de padrões e a identificação de possíveis falhas, possibilitando que a manutenção seja realizada exatamente quando necessário. Essa abordagem não só reduz os custos associados a paradas inesperadas, mas também melhora a eficiência operacional, uma vez que os equipamentos são mantidos em condições ideais de funcionamento.
A indústria 4.0 é outra tendência que está transformando a manutenção e a instalação industrial. Com a integração de tecnologias digitais como inteligência artificial (IA), aprendizado de máquina e automação, as fábricas estão se tornando mais inteligentes. Isso se traduz em operações mais eficientes e na capacidade de monitorar e gerenciar equipamentos e processos de forma remota. A implementação dessas tecnologias permite um melhor planejamento de manutenção e otimização de processos, contribuindo para um aumento considerável em termos de produtividade e redução de custos.
Outra tendência crescente é o uso de realidade aumentada (RA) e realidade virtual (RV) para a manutenção e instalação. Essas tecnologias permitem que os profissionais visualizem informações em 3D e simulações em tempo real do processo de instalação ou reparo. Por exemplo, com óculos de RA, os técnicos podem receber instruções sobre o equipamento diretamente em seu campo de visão, facilitando a execução de tarefas complexas com maior precisão e segurança. Essa abordagem não apenas melhora a eficiência, mas também reduz o tempo necessário para os treinamentos, pois os profissionais podem praticar em ambientes virtuais antes de realizar o trabalho real.
A digitalização e a gestão de dados também estão conquistando espaço nas empresas industriais. As organizações estão cada vez mais cientes da importância dos dados para a tomada de decisões estratégicas. Com a coleta e análise de dados, as empresas podem obter insights valiosos sobre suas operações, identificando ineficiências e oportunidades de melhoria. Sistemas de gestão de manutenção assistida por computador (CMMS) são essenciais para a centralização de informações e o planejamento proativo, contribuindo para uma melhor gestão do ciclo de vida do ativo.
Também é importante notar a crescente ênfase na manutenção verde. À medida que as empresas buscam reduzir sua pegada de carbono e melhorar a sustentabilidade, práticas de manutenção que utilizam energias renováveis e reduzem o desperdício estão se tornando cada vez mais prevalentes. Isso inclui a análise do desempenho energético das máquinas e a implementação de melhorias que reduzam o consumo de energia, contribuem para um ambiente mais sustentável e, ao mesmo tempo, reduzem custos operacionais.
A formação e qualificações contínuas dos profissionais também estão se tornando uma prioridade. Com as rápidas mudanças tecnológicas, é essencial que os profissionais de manutenção e instalação industrial estejam atualizados com as novas ferramentas e técnicas disponíveis. Programas de capacitação e educação continuada são importantes para garantir que as equipes estejam bem preparadas para lidar com a evolução do setor. Dessa maneira, as indústrias não apenas mantêm um alto padrão de qualidade, mas também garantem segurança e eficiência nas operações.
Outra tendência em crescimento é a utilização de robótica e automação nas operações de instalação e manutenção. O uso de robôs para tarefas repetitivas ou perigosas não apenas reduz riscos para os trabalhadores, mas também libera as equipes para se concentrarem em tarefas mais estratégicas. A automação está se tornando uma ferramenta valiosa para aumentar a precisão e a eficiência em tráfegos agitados e manutenção industrial em ambientes desafiadores.
As tecnologias de impressão 3D também estão começando a fazer parte do cenário da instalação industrial, permitindo que as empresas produzam peças sob demanda. Isso pode reduzir significativamente os tempos de espera para obter peças de reposição, resultando em menos paradas de equipamento e maior eficiência geral. A impressão 3D tem o potencial de transformar a forma como as indústrias pensam sobre controle de estoque e fornecimento de peças, oferecendo maior flexibilidade e opções personalizadas.
Além disso, a colaboração entre empresas e fornecedores está se tornando cada vez mais importante. A criação de parcerias estratégicas e alianças tem ajudado as empresas a acessarem novas tecnologias e práticas de manutenção. Trabalhar em conjunto com uma empresa especializada em montagens pode facilitar a troca de informações e experiências, melhorando a eficiência e a eficácia na instalação e manutenção de sistemas industriais.
Em resumo, as tendências futuras em manutenção e instalação industrial são impulsionadas por inovações tecnológicas que visam melhorar a eficiência, segurança e sustentabilidade das operações. A adoção de manutenção preditiva, a digitalização e gestão de dados, o uso de RA e RV, o foco na manutenção verde e a qualificação contínua dos profissionais marcam um novo rumo para o setor. Ao se adaptarem a essas tendências, as empresas estarão mais preparadas para enfrentar os desafios do futuro e garantir uma operação mais eficiente e sustentável.
Em suma, a manutenção e instalação industrial desempenham um papel crucial na performance e segurança de qualquer operação industrial. Ao compreender a importância desses processos e adotar as diversas estratégias de manutenção, as empresas não apenas minimizam o risco de falhas, mas também aumentam a eficiência e prolongam a vida útil dos seus equipamentos. As inovações tecnológicas e as tendências emergentes, como a manutenção preditiva e o uso de realidade aumentada, estão transformando a maneira como as indústrias encaram esses desafios. Ao investir em boas práticas e na formação contínua da equipe, as empresas estarão mais preparadas para enfrentar o futuro, garantindo não apenas a segurança no ambiente de trabalho, mas também a satisfação do cliente e o sucesso nos negócios. Portanto, é fundamental que gestores e profissionais do setor reconheçam o valor de uma abordagem proativa em manutenção e instalação, promovendo assim um ambiente produtivo e seguro para todos.